Historical Insights into Lean Manufacturing
While rudimentary principles of lean manufacturing trace back centuries, it gained prominence with Benjamin Franklin's emphasis on waste reduction. This evolved into Frederick Winslow Taylor's ‘Principles of Scientific Management’ in 1911, promoting methodical productivity enhancement. However, the actualization of these principles into a comprehensive approach came from Shigeo Shingo and Taiichi Ohno at Toyota. Their Toyota Production System (TPS) emphasized ‘pull’ (demand-driven) over ‘push’ (forecast-driven) production.
The transition from ‘just-in-time’ manufacturing in the 1980s to lean manufacturing in the late 1980s and 1990s was marked by John Krafcik's 1988 article, which emphasized the superiority of lean manufacturing in terms of productivity and quality.
As a classical example: Let’s take Ford. In its quest for efficiency, Ford has integrated lean principles into its production processes, minimizing waste, and maximizing value. The assembly line, a brainchild of Ford, mirrors Adam Smith’s ‘Division of Labour’ from 1776, which prioritized task-specific roles to enhance efficiency. Lean methods, while stemming from production, have seamlessly transitioned into service provisions, underscoring their universal applicability.
What is Lean manufacturing?
At its core, lean manufacturing zeroes in on waste elimination, streamlining processes to offer the highest value to customers.
Yes, you heard it right. Lean processes are focused on illuminating waste, not just like garbage we used in our every day life, but in more broad sense. Waste isn’t restricted to mere materials; it encapsulates underutilized talent, excessive inventories, and ineffective processes.
Waste is antithetical to productivity. The umbrella of waste includes idle workers, unused materials, and poor processes. Lean manufacturing, hence, is not just about profitability; it plays a pivotal role in amplifying customer satisfaction through, by bringing these 4 benefits:
- Waste Eradication: Removing non-value-adding components.
- Quality Enhancement: Catering to dynamic customer needs, giving businesses a competitive edge. Rework is waste. Additional quality checks that can be excluded are waste.
- Cost Minimization: Efficient resource and material management eliminate unnecessary storage costs.
- Time Management: Addressing inefficient practices to speed up delivery.
Core Principles of Lean Manufacturing
- Value: Understand what the customer perceives as value that they are willing to pay and strive to provide it. This value is then created by the manufacturer or service provider who should seek to eliminate waste and costs to meet the optimal price for the customer while also maximising profits.
- Value Stream Mapping: Analyze the entire production lifecycle from raw materials to disposall to identify and eliminate wasteful steps, in materials, storing, additional works that doesn't create value(lets say, rework doesn't create value for the customer because product should be finished from 1st try).
- Flow: Establish uninterrupted processes that enhance efficiency. It should be constant flow of materials and this is where optimal batch size of one pcs comes in handy.
- Pull System: Begin production processes in response to actual demand from the customers, rather than production based on forecasts. Its opposite to push system when we plan everything around how much products we plan to ship, that could lead to additional costs. A pull system only acts when there is demand.
- Perfection: Continually refine and processes improvements, aiming for the optimal workflow and finding bottlenecks. is also known as Kaizen. In Lean manufacturing improvement projects don't stop and start again as soon as old project is finished and team is available.
I think you can already see many similarities to modern product management. Lets go further in Lean.
The Eight Wastes
Remember, we focused on maximizing value added time, and reduce time that doesn't bring any value (waste).
Originally, Toyota identified seven wastes that detract from value:
- Unnecessary transportation of product - transportation from one place to another for further processing doesn't create value for the customer.
- Excess inventory - Time while we store components doesn't bring value to customers
- Unnecessary movement of people, machinery - Bad optimized work environment. For example workers need to walk from one station to another to take tools that they need.
- Waiting times - Waiting for processing while in batch doesn't bring any value.
- Over-production - Too many products being produced that are not required.
- Over-processing - Adding too much features that customer doesn't need
- Defects - additional works required for scrap and rework. Customer pays for product finished from 1st time. All reworks are pure waste.
Subsequent lean practitioners added an eighth: Unused talent and ingenuity.
These wastes fall under three categories (don't need to remember actual words):
- Mura (Unevenness): Fluctuating demand.
- Muri (Overburden): Resource misallocation.
- Muda (Process-Related Waste): Non-value-adding work.
Central concept of lean manufacturing:
Central topics in lean manufacturing are the concepts of value-add time and non-value-add time.
What is Value-Add Time?
Value-add time (VAT) pertains to the period wherein a product is undergoing a change that transforms it closer to its final form, and for which the customer is willing to pay. Essentially, it's the time spent on activities that add value to the product. The aim in lean manufacturing is to maximize value-add time while minimizing non-value-add time.
Example: In car manufacturing, the process where the engine is being installed into the vehicle constitutes value-add time. The customer gets a tangible benefit from this activity, as a car without an engine would be non-functional.
Its important to remember that value add time considered in scales of 24 hours, 7 days a week. Nights, when there is no operations are done, considered to be waste.
What is Non-Value-Add Time?
Non-value-add time (NVAT), often deemed wasteful, encompasses the durations when the product is not being actively worked upon or when it's undergoing procedures that the customer isn't directly willing to pay for. This time does not contribute to the form or function of the product.
Example: If after the engines are installed, the cars are left waiting in a queue for the next assembly process, that waiting period is non-value-add time. Another example is the time spent moving parts from one workstation to another without any productive transformation.
This concept is very close to Agile thinking, where we try to benefit from short iteration and adapt to new information
Example of value add analysis (and how much time we really spend bringing value) :
For better understanding what is value add time, and what is not, lets look into hypothetical example:
Lets look into car assembly factory from 60th that is not optimized and not operate in max capacity.
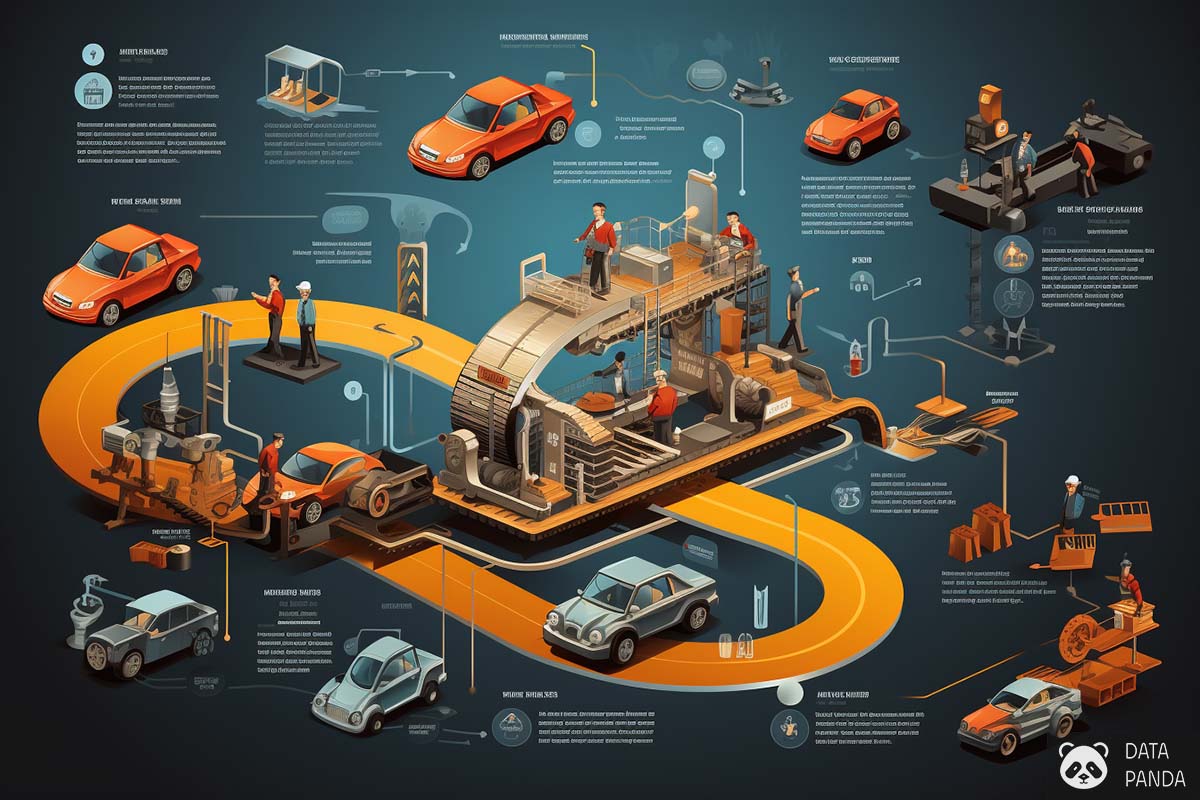
Case: The process of assembly occur during an 8-hour working shift (e.g., 9:00 AM to 5:00 PM). The duration for each step will be adapted based on the batch size to ensure that they roughly consume the same amount of time (takt time approximately 2 hours).
Definitions:
Value add time: Time when works are done on one pcs of equipment that is tranformed to values
Processing time: Time that batch is in process, but no value is created.
Total time: Value add time + processing time for the process step.
Batch size: Number of cars in a process step(station) at the same time, while work is done on one pcs. Batch released to next step only when all cars in this batch are finished.
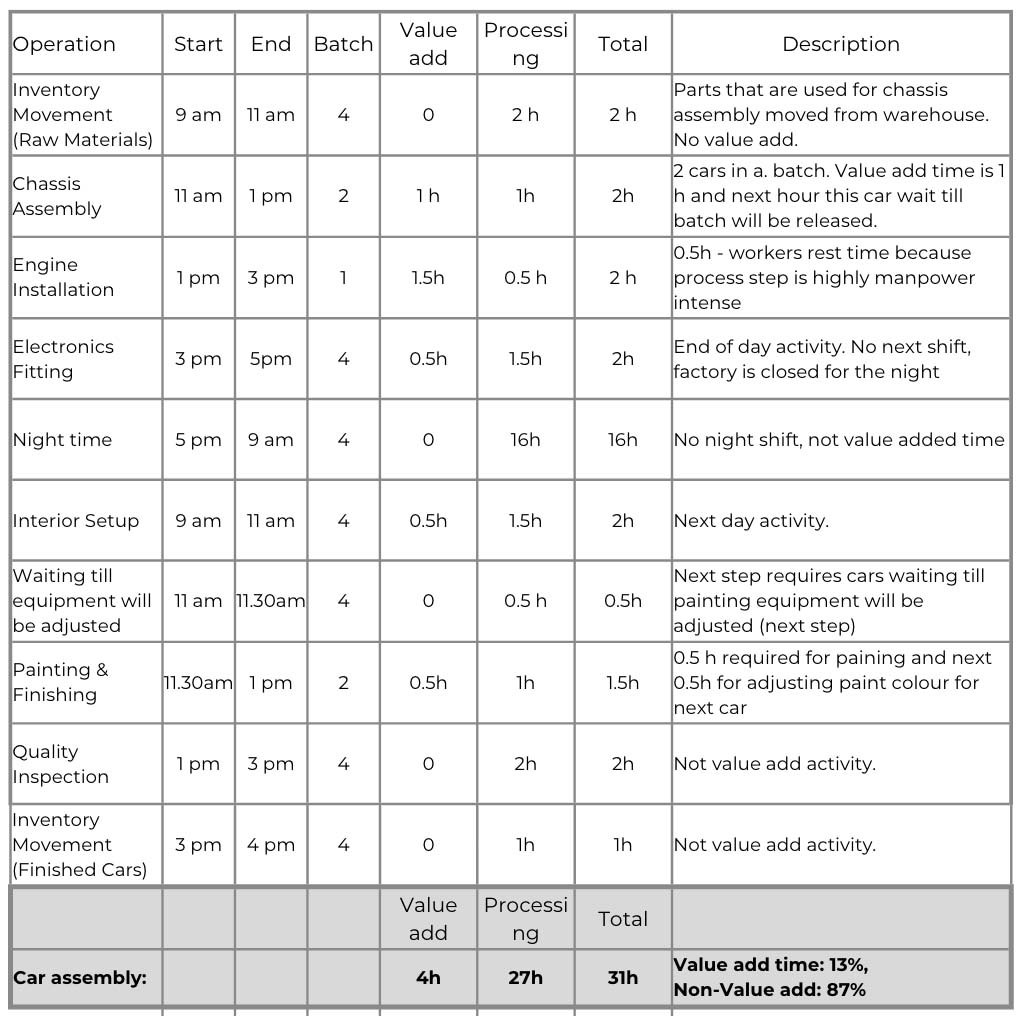
As you can see, in this process:
Value add time - 13%
Non - Value add time - 87%
It is quite common that value add time could be 1 digit number, especially when you work in large batches. That is why lean manufacturing try to achieve batch size 1, and you can see also method of limiting number of items on scrum board in scrum to limit "batch" during product development.
P.S some of questions I got:
- Quality inspection is controversial topic: While it doesn't contribute to value for customer, it helps factory to reduce cost of poor quality, thus in actual life you should have this step. To design the process that doesn't require quality control steps is very difficult and these steps (even if they don't benefit customer in "lean nerd" perception) should exist.
- When batch size varies from 4 to 1, in constant takt time, it means there are several stations working on the same 4 cars. So all of them have value add time at the same time.
- Night time, weekends, holidays and any non working time considered non value add time and should be considered in calculations.
Common techniques (common for product management and manufacturing).
In this list I will give some of the techniques that are used in lean manufactoring and that you can see in product management. It might give ideas how to improve your products.
- Value Stream Mapping (VSM)
Description: A visual representation that displays all the steps required to deliver a product or service to the customer. We create a scheme how value is added from beginning to the end.
Example: In a car manufacturing process, VSM may illustrate the flow from raw material procurement to assembling components, all the way to final quality checks before delivery.
In Product Management: Used to visualize the process of product development, identifying bottlenecks, wasteful activities, or steps that don't add value to the product or user.
- Kaizen (Continuous Improvement)
Description: A culture where employees at all levels are continuously seeking ways to improve operations.
Example: An assembly line worker might suggest a change in tool placement that shaves off a few seconds from the manufacturing process.
In Product Management: Product teams adopt a culture of continuous improvement by regularly iterating on product features, analyzing user feedback, and making necessary refinements. Kaizen is in the heart of Agile ideas.
- Kanban
Description: A visual system to control production quantities and ensure that only what's needed is produced.
Example: A whiteboard displaying cards representing tasks. As tasks are in process, they move from 'To Do' to 'In Progress' to 'Done', ensuring a smooth workflow and preventing overproduction.
In Product Management: Widely adopted in Agile product development, the Kanban board helps product and development teams visualize workflow, control work-in-progress, and maximize efficiency. Tools like Trello, Jira, and Asana often have Kanban-style boards.
- Poka-Yoke (Mistake Proofing)
Description: Designing processes in such a way that errors are either eliminated or immediately detected.
Example: Connectors on your devices allowing to connect only one way. Other implementation - different size of connectors when you assemble something. So you can't connect wrong parts together.
In Product Management: Techniques are implemented to ensure that users can't make easy mistakes when using a product. For instance, in software applications, this might involve form validation checks, confirmatory prompts before critical actions, or intuitive user interface design.
- Heijunka (Load Leveling)
Description: A technique used to balance production volume and type, thereby avoiding batching.
Example: If a factory produces two products, A and B, rather than producing them in separate batches, it might switch between A and B to respond more flexibly to demand.
In Product Management: Used in the context of balancing feature releases. Instead of releasing a large batch of features at once, teams might release them incrementally to manage load and ensure stability.
- Quality Function Deployment (QFD)
Description: This tool is from lean six sigma approach, but still commonly used. It is a structured approach used in Lean Six Sigma to convert customer needs (often referred to as the "Voice of the Customer" or VOC) into specific technical requirements for a product or service. It is visualized through the "House of Quality", a matrix that facilitates understanding the customer's desires and translating them into actionable design and process characteristics.
Example:Team design coffee machine. In surveys they learned what is important to the customers (CR), then they come up with potential technical solutions(TD) or attributes that affect CR. They create relation matrix between CR and TD. The company will rate the TDs based on feasibility, cost, and alignment with CRs and prioritize the ones that should be implemented.
In Product Management: Understanding which features or attributes to prioritize becomes crucial. QFD's relationship matrix is similar to features prioritization in product roadmaps.
Just like in QFD, modern product management emphasizes deep customer understanding. Through interviews, surveys, and analytics, product managers seek to understand the VOC and address it.
QFD and House of Quality is a more complicated approach compare to prioritization matrix used in product management, however they are trying to solve same problems.
- Takt Time
Description: The maximum amount of time allowed to produce a product in order to meet customer demand.
Example: If customer demand is 400 units per day and the production time available is 800 minutes, then the takt time is 2 minutes per unit.
In Product Management: Applied when considering the frequency of feature releases or updates. Ensuring that there's a consistent rhythm or "heartbeat" to how often new value is delivered to users can be crucial, especially in SaaS (Software as a Service) environments. Also when we think about 2-4 week sprints in Scrum.
- Standard Work
Description: Clearly documented and standardized procedures for each process, ensuring consistent output.
Example: A checklist or manual detailing the exact steps and best practices to assemble a particular component.
In Product Management: Ensuring consistent processes in product development cycles. This could involve regular sprint reviews, documented user story creation processes, or consistent UI/UX design protocols. Again, defined roles and artifacts for Scrum.
- Root Cause Analysis (RCA)
Description: A method used to identify the root cause of problems or faults. Often used with 5 whys technique.
Example: If a machine breaks down, rather than just fixing the immediate issue, RCA would delve deeper to find the underlying cause, such as a lack of regular maintenance.
In Product Management: When issues or unexpected behaviors occur post-release, product managers and their teams will dive deep to find the root cause, ensuring not just a superficial fix but a solution that addresses the foundational problem.
Common techniques (common for manufacturing, but not so common in product management).
While previous list consist of many tools that you are actually using every day, there are still many not so commonly used tools, but again, some companies found a way to adapt it. To reduce length of this blog post, you can read them in other blog post.
Conclusion
While many product managers might not explicitly recognize their adoption of tools from lean manufacturing, there exists an intrinsic connection between the two realms. This overlap underscores the universal applicability of lean principles in driving efficiency, optimizing processes, and delivering value. Regardless of the domain—be it manufacturing or product management—the end goal remains the same: to streamline operations and create products that resonate with the end-user. Thus, acknowledging and harnessing this interconnectedness can provide a robust framework for continuous improvement in product management endeavors.